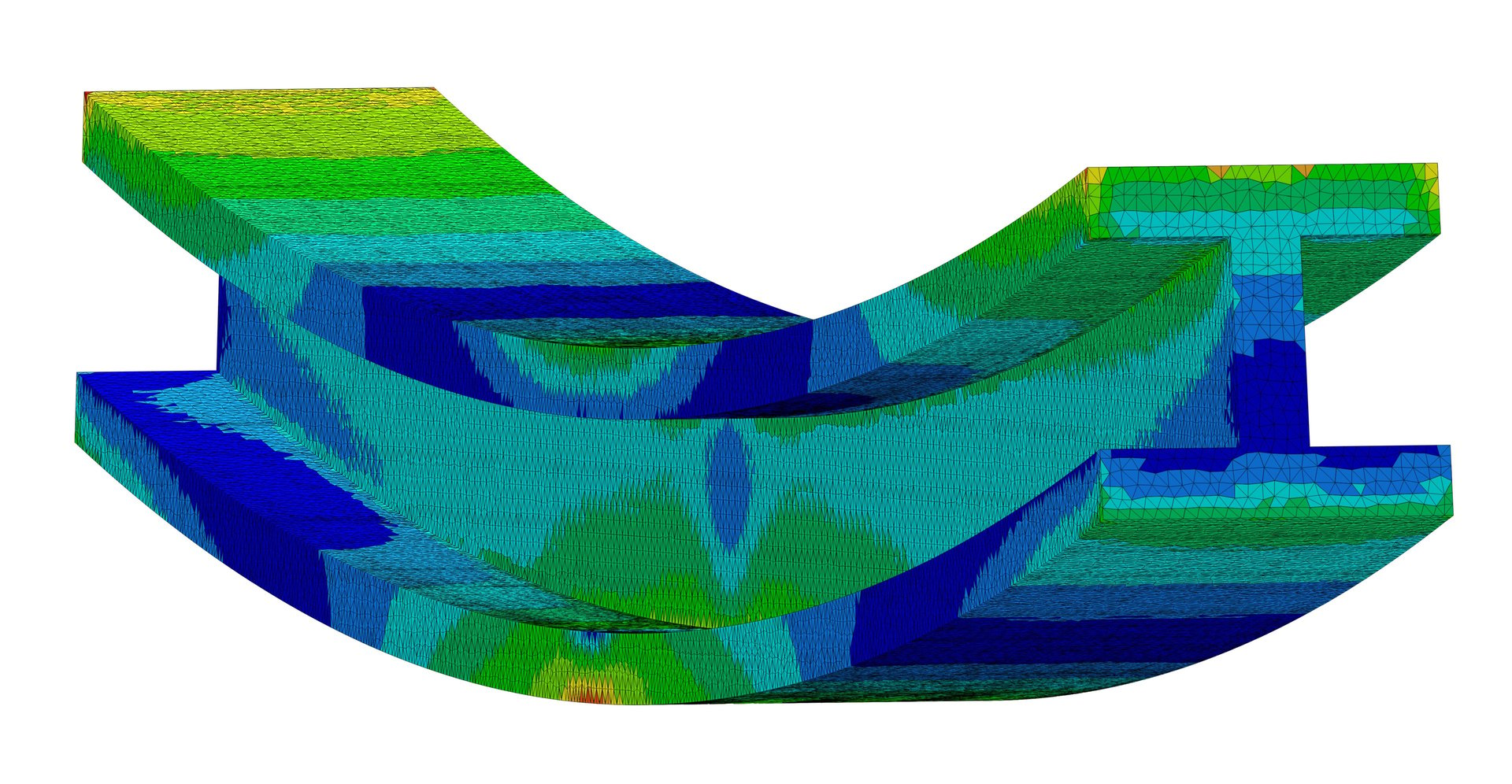
Mechanical Analysis
Precision-driven FEA is at the core of Concentus Systems Design. We leverage best practices in Finite Element Model generation to deliver accurate and insightful structural analyses, empowering informed design decisions for optimal performance and reliability.
Modal Analysis
Modal Analysis allows us to delve into the dynamic characteristics of structures, revealing their natural frequencies and mode shapes. This insightful technique aids in optimizing designs for enhanced performance and reliability.
Static Analysis
Static Analysis is the cornerstone for evaluating structures under constant loads. This is also useful when specific loads or pressures are provided from a higher level Dynamic analysis. We meticulously model and analyze systems to ensure they meet performance requirements and withstand static forces seamlessly.
Sine Vibration
Sine Vibration analysis enables us to study structures subjected to sinusoidal vibrations, and the level of response at particular critical frequencies. Whether you have predefined specifications or need assistance defining environments, we tailor the analysis to meet your specific requirements.
Buckling
Buckling analysis is performed to determine critical buckling loads of all structural components. This analysis, used in conjunction with load predictions from other dynamic analysis cases is used to determine buckling margins of the design.
Random Vibration
Expertise in Random Vibration analysis equips us to assess structures facing unpredictable loading conditions. This includes scenarios like components mounted to a surface excited by acoustic noise, aerodynamic flow, or road noise.
Shock
In Shock Analysis, we employ Shock Response Spectrum (SRS) or transient analysis, depending on your requirements, to evaluate structures under sudden, high-impact loading. Our precise modeling addresses critical aspects, providing a thorough understanding of structural responses.
Thermal
Thermal analysis is employed to evaluate stresses of components resulting from thermal expansion, and to quantify and validate pointing and stability performance of hardware under extreme thermal environments.
Loads & Dynamics
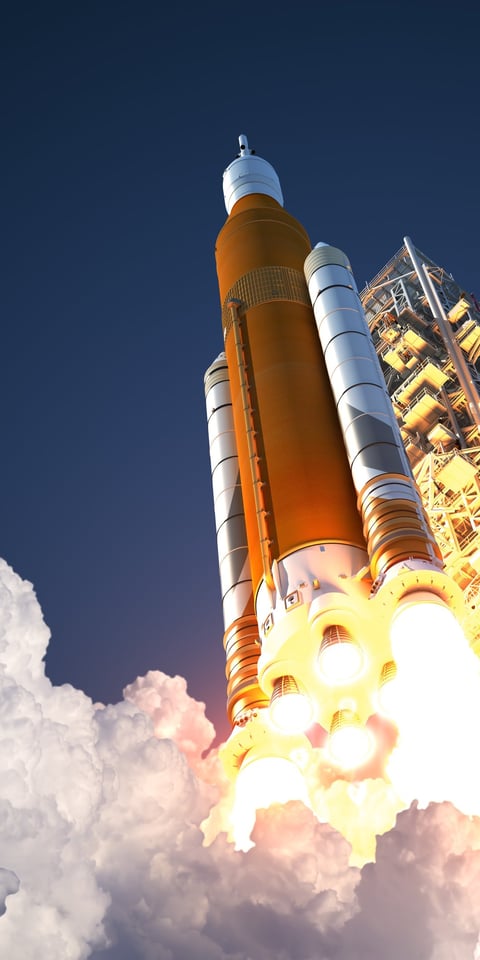
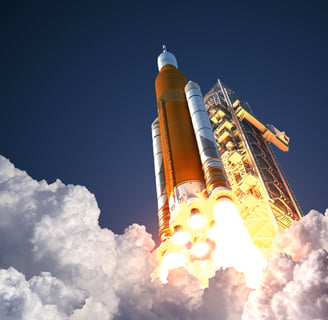
Stress Analysis
At times, the results from the dynamic simulations lead straight to the end result. Other times that is just beginning. In depth stress analysis takes a careful scrutinizing of results from model predictions and knowing how use the data to determine the final stress states of the components, and finally the component margins of safety.
Post Processing Simulations
By understanding which details to capture within the model and which to refine in post-processing, we achieve a delicate balance between accuracy and efficiency. This approach yields robust predictions without necessitating a supercomputing army, saving you time and resources.
Model results are run through post processing routines to determine :
Final stress states of delicate features
Laminate stresses and their implications
The integrity of bolted and bonded joints
Component fatigue behavior over time
Stresses in PWB components
Other critical details too intricate for system-level modeling

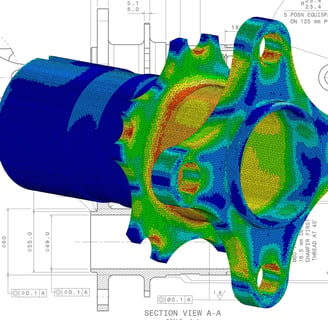
Other Modeling Specialties
Advanced Contact Models
Our advanced modeling techniques include the implementation of contact models, addressing complex scenarios such as pressure-sensitive thermal joints, load distribution around a seal, and the intricate performance characteristics of bolted joints. Whether evaluating friction effects or ensuring the optimal functioning of interconnected components, our contact models enhance the accuracy and reliability of your simulations.
Super Element Models
In scenarios demanding efficiency or protection of proprietary design information when sharing FE models with external customers or suppliers, we utilize super element models. These can expedite existing analyses or be shared externally without divulging sensitive details.
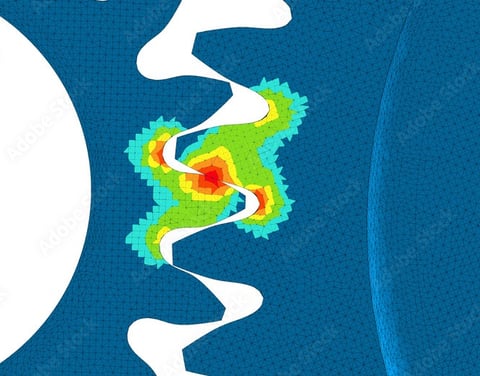
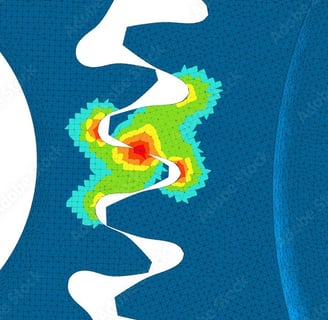
Contact Us to Discuss Your FEA Needs
Comprehensive Expertise.
Cutting-Edge Tools.
Customized Solutions.
Unlocking Engineering Excellence:
Contacts
inquiries@csdaero.com
(760) 300-3770